GEA Doubles the Drive Power of Hygienic Pump
GEA supplements its GEA Hilge Hygia range with a 45 kilowatt motor, thereby expanding the hygienic pump’s performance spectrum to a flow rate of 180 cubic meters per hour. The new version is also suitable for demanding pharmaceutical applications, particularly because the use of high-quality, no-cast materials in CIP- and SIP-capable special pumps is a critical factor in the production of life science products.
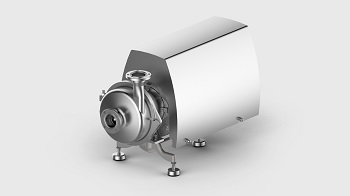
GEA Hilge Hygia
A 60 percent increase in conveying capacity
The GEA Hilge Hygia 45 kW is an end-suction centrifugal pump from the “Hygia” premium line, which has a decades-long proven track record in sterile applications thanks to its electropolished surfaces, high-quality sealing materials and flexible designs. “Our successful pump packs more horsepower under the hood”, says Martin Zickler, product manager for hygienic pumps at GEA. “The 45 kilowatt motor allows us to deliver 60 percent more flow rate than before.” Instead of 110 cubic meters per hour, the pump now delivers 180 – a quantum leap that enormously increases the performance range of the hygienic pump.
Simplified spare parts handling
The remarkable thing is that GEA covers the performance range with just two sizes. “Our customers are used to achieving this performance range with several different sizes. In practical terms, this means that they require numerous mechanical seals and different O-ring sets for operation. Managing such a spare parts inventory requires considerable logistical effort from customers. We can now reduce that considerably,” says Zickler. Along with the pharmaceutical industry’s demands for hygiene, investment and operating costs for process technology are also on the rise. According to Zickler, maintenance and spare parts replacement are also significant cost factors in this sector.
Hygienic pumps for the highest water quality
The GEA Hilge Hygia has a long-standing reputation as a hygienic pump for food and beverage processing. However, GEA sees great potential in pharmaceutical manufacturing, particularly due to critical fluid characteristics such as lack of lubricating properties and the stringent regulations that make pump designs more challenging. “The main applications are, for example, WFI distribution systems (WFI = water for injection),” explains Zickler. In addition to its high-performance pumps, GEA also delivers smooth and cavity-free hygienic design and reliable technical documentation.
Non-cast parts that are easy to clean
In order to facilitate cleanability in hygienically sensitive applications, GEA uses forged, deep-drawn and milled components instead of castings for media-contacting parts. “Because of the risk of blowholes, cast parts are particularly undesirable in the pharmaceutical industry. Cleanability would be reduced, thus making it difficult to obtain the 3-A certification,” says Zickler. However, both aspects were important parameters for GEA in the development of the pump. All materials have therefore been carefully selected for their use in hygienic processes. The casings are made of forged CrNiMo (1.4404) and have blowhole-free, smooth surfaces. GEA engineers adapted the design of the shaft and impeller – which must transfer the now higher forces – to match the powerful 45-kilowatt motor using a high strength CrNiMo 1.4462 duplex steel.
Like the entire hygienic range, the GEA Hilge Hygia 45 kW also carries the 3-A seal. “This is the prerequisite for our North American business, which we want to focus on this year. Our customers in the U.S. are already waiting for our high-performance Hygia due to the larger production quantities processed there,” explains Zickler.
Source: GEA Group Aktiengesellschaft