Extension of the Vacorex and Thermorex Series for Higher Throughputs and Pressures
Maag unveils new, low-pulsation, retrofittable versions to boost performance.
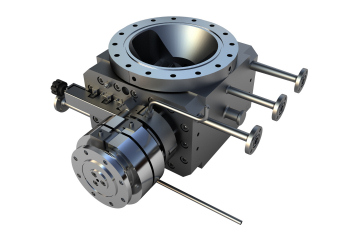
Reliable and gentle extraction: vacorex discharge pump from Maag for applications in the polymer industry (Image: Maag)
Maag is now transferring its experience of extrusion technology to high-performance gear pumps for the polymer industry. Maag is offering the vacorex (discharge pumps) and thermorex (transfer pumps) series with immediate effect in performance classes GP, HV and HP for the manufacture of polymers.
The new versions have been designed in response to specific requirements in terms of throughput and pressure increases. As the pioneer in pumping technology, Maag is once again delivering maximum availability over a broad sphere of operation and spectrum of performance. High reliability, global support and tailor-made solutions for the customer’s polymer manufacturing application are the focal hallmarks of the new developments from the experts from Oberglatt.
The vacorex discharge gear pumps
Assemblies are needed in polymer processes that are able to extract low and high-viscosity plastic melts gently from reactors and degassing systems. The production process takes place directly below the reactor. A constant and precise filling behaviour, coupled with short standing times, predestine this series for use in the polymer industry. The high level of efficiency and long service life increase the overall efficiency and availability of the production plant. The series comprises sizes 45 to 560.
The thermorex transfer gear pumps
The thermorex series also focuses on the gentle conveying of carrier media of varying viscosities for polymer processes. A special gearing with a low squeeze factor is one design feature that makes the thermorex transfer, booster or metering gear pump so ideal for polymer processes. A high degree of efficiency with constant and precise transport – even at high outlet pressures – are also guaranteed with this series. The pumps are integrated as transfer or booster models into the transfer pipe (“in-line”) or directly onto the mixer, kneader or extruder. The series comprises series sizes 45 to 360.
Low-pulsation and performance-orientated
One really striking feature is the new generation’s compact construction. Optimised inlet geometries ensure excellent filling properties. The design of the flow channels has been optimised to encourage flow. The carrier materials can be heated continuously to up to 350°C in order to influence their viscosity. This yields viscosities of up to 20,000 Pas. A special gearing system with extremely low squeeze effects allows polymer melts to be handled gently. The shaft seals, gear and bearing technology from Maag ensures minimum friction and guarantees an excellent level of efficiency. And last but not least, the two series offer low-pulsation transport even at high differential pressures.
Reliability is the key – GP pump version
The new GP version delivers a higher degree of pump efficiency than ever before. The pump bearings and gear geometries have also been modified in order to increase the pump’s emergency running properties. The GP version is available for all sizes in both series. The GP version is used for standard applications with pressure differentials of up to 250 bar and is therefore designed for a wide range of uses.
Optimised process technology thanks to HV pump version
The HV version offers users higher material throughputs. Compared to the GP version, Maag’s specifications cite a 25% higher filling volume. The compact construction also means a small footprint, like the GP basic version. All this is made possible thanks to a reduced process pressure of up to 200 bar differential pressure. In the standard range, it is available from size 140 upwards.
Achieving peak performance with the HP pump version
The HP version s design has been created to withstand process pressures of up to 300 bar differential pressure, allowing the highest throughput volumes of all of the versions. It is also available from size 140 in the standard Maag range.
Keyword retrofit
According to Maag, the combination of the pump design and process technology experience is the only one of its kind in the world, and elevates it to reference class. Some of the internal parts have been designed so that they can be interchanged between the GP, HV and HP versions. The new versions, says Stefan Kalt, Head of Pumps Business Unit Polymer at Maag, are significantly increased the throughput. For the polymer manufacturers the retrofit to these versions is therefore very interesting. As a result, the two vacorex and thermorex series can be offered in formats that have been specifically tailored to the throughput and process pressure of the customer s application.
Source: Maag Pump Systems AG