Energy Efficient Vacuum Systems for Furnace Industry and Metallurgy
The highest priority for vacuum pumps and systems certainly is the reliable delivery of the required vacuum levels. The trouble-free operation of the vacuum system is a must. The growing pressure to save energy is not allowed to restrict the productivity of the plant. Still, vacuum pumps and systems must be designed following the “state of the art” regulations.
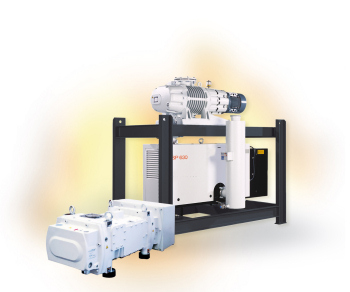
Dry-compressing vacuum systems for use at furnaces (Image: Oerlikon Leybold Vacuum)
Fighting against global warming and increasing greenhouse gas concentrations, the regimentation of CO2 emission are the justification for the European Commission to set up the European Directive 2005/32/EC. This and several amending directives describe a framework of eco-design requirements for energy using products asking for increased efficiencies. New standards and norms have been written and others have been updated which now need to be considered in new product engineering projects. Furthermore, energy costs are rising constantly and will continue to rise in the future.
Considering these aspects the design of modern furnaces has changed recently. New designed vacuum furnaces are operating much more efficient than older furnaces. Also modern steel degassing plants use more and more mechanical vacuum systems instead of energy-wasting steam ejector systems. Also here, modern vacuum pumps and pump systems, designed to support these energy saving attempts, have proven their capabilities.
High reliability can be reached by using traditional technologies as e.g. oil-sealed rotary piston or rotary-vane pumps, roots blowers and diffusion pumps, but also also more modern technologies such as dry screw pumps already have a proven track record to work most reliable even under harshest conditions. Today’s standard dry pumps are screw pumps with variable pitch rotor design. Continues compression along the rotor length minimizes the energy demand. Older technologies with constant screw pitch or even dry pumps based on multiple stages of roots- or claw type rotors, have significantly higher power consumption due to design and pumping principle. But even the plurality of today’s screw-pumps with variable pitch differs a lot from each other. Most pumps of the 600 m³/h class demand app. 10 kW power at typical furnace operation pressures below 1 mbar, which is a clearly higher value as those of a comparable rotary-vane pump.
The Dryvac pump series of Oerlikon Leybold Vacuum are optimized with regard to the mechanical rotor design, the electrical motor concept and by selection of a perfectly matched build-in frequency converter.The achieved result in energy saving is substantial, as the pump only consumes 6.9 kW at 1 mbar, is even more energy efficient than a rotary-vane pump and therefore is the new bench mark for power consumption in the market. The build-in frequency converter also offers potential for additional savings and higher process control. Many process steps do not require “full-power” suction speed, especially during operation at rougher pressures, e.g. during carburizing.
Soft start and ramping functionality can be realized with the variable frequency drive. Chamber pressure can be controlled by varying the rotational speed. The customer can even realize a process specific “standby condition” considering certain valve positions to save for example the volume of supplied Nitrogen. Next to these environmental issues, the modern design of the Dryvac eliminates sensitive components as shaft- seals or couplings which clearly increase robustness and reliability of the pump.
Modern designed pumps improve the energy consumption, but several measures can also improve the situation with traditional pumps. Oil-sealed pumps and roots-pumps need to be equipped with newest standard IE2-motors and can be operated with frequency converters to deliver just as much suction speed as required. Oil-diffusion pumps can be equipped with innovative control-systems which can identify the actual power demand and regulate the power supply of the heaters accordingly. These measures diminish the power consumption of a diffusion pump by more than 30 per cent.
Today, all modern vacuum technology options should be considered for choosing the right vacuum solution. Modern system solutions are robust, highly reliable, environmental friendly and cost efficient.
Source: OC Oerlikon Management AG