Efficiency and Availability Depend on the Quality of Design Data
As is usually the case at ACHEMA, producers of pumps, fittings and seals will be the largest contingent of exhibitors at the show, which will be held in Frankfurt / Main, Germany, from May 15 – 19, 2006. 850 of the 4,000 exhibitors will be from this sector. As always, the one thing that visitors will want to know is how plants can pump media and control the flow of material safely and reliably with ...
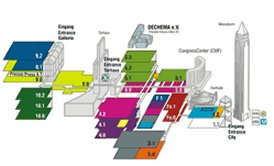
... zero emissions and above all, how this can be done in the most cost-effective manner. Around 200,000 visitors from 100 countries are expected to attend the show, including 40,000 potential decision makers.
In what is admittedly an extreme case, pump manufacturer KSB is supplying the biggest cooling water pumps it has ever made to a new coal-fired power station in Yuhuan, China. Each of the eight 130 ton units can pump up to 16,000 liters of cooling water per second, drawing 4.6 MW of power from the grid. But even small industrial pumps consume a lot of energy. Operators who were not aware of this in the past or simply didn’t want to know are now in for a shock when they look at their spiraling utility bills. Electricity prices have been rising steadily at double-digit rates in Germany since 2002 (despite deregulation). Electricity continues to become more expensive throughout Europe. In light of these developments, pump system operators are looking even more closely at the overall efficiency of their pumps and motors.
Even with older pumps, it is worth looking at the pump and the operating environment to find ways of counteracting the increased cost of electricity. The Pumps + Systems Association at the German Engineering Federation (VDMA) believes that energy savings in the region of 20 % – 30 % are realistic. The Group has now joined forces with the German Energy Agency (dena) to launch the “System Efficiency” campaign.
A framework is being put in place to help industrial and commercial operators analyze and reduce the amount of energy used by their pump systems. Industrial partners are contributing to the project, including pump manufacturers Grundfos, KSB, Sulzer and Wilo. The goal is to define ways to save energy and demonstrate the economic payback of energy saving measures, provide information, analyze lifecycle costs and generate a wide range of fact sheets. At ACHEMA 2006, which will be held from May 15 – 19 in Frankfurt am Main, pump manufacturers will present a range of strategies and practical solutions for reducing the energy consumption of industrial pumps.
Ensuring availability
Saving energy is important. However, pumps and other “auxiliary” equipment must do one thing above all in an industrial process, namely they have to run and run and run. From the process engineering point of view, availability is crucial and it overshadows other considerations.
So what can equipment producers and operators do to prevent downtime? Redundancy is one possible answer, for example a reserve pump. More elegant solutions are now available which make increasing use of electronics and sensors. Moving mechanical parts will also be subject to wear no matter how good and durable the components are. This makes it all the more important to detect wear as early as possible.
It is also important that operators sit down with suppliers at a very early stage to discuss the operating requirements to ensure that the supplier is aware of the load and stress factors. It is always better to avoid critical operating conditions by conducting good up-front planning for the entire system than to simply find a reliable way of detecting a “bad” system.
Again and again, practical experience has shown that bad actors are usually pumps that are too big for the job. Nobody denies this in principle, but everyone knows that “good planning” presents a very significant challenge when basic information on the media and the process is not available when pump specifications are drawn up.
Energy conservation is not the only reason why a centrifugal pump should run at or near the operating point. Mechanical stress is also an important consideration. When pumps are not operating near the operating point, radial forces begin to put stress on the bearings and mechanical seals, and cavitation increasingly becomes a problem. This makes it important to avoid adding in a safety factor in the pump specification.
If a pump is designed correctly, failure will only occur due to early or random failure or as a result of out-of-spec operating conditions. Normal wear is another possible cause of failure (end of life).
Monitoring and early fault detection
The wish of every process engineer and maintenance technician is to have a way of detecting equipment faults before downtime occurs. Action rather than reaction is the goal. A range of vibration, pressure, temperature and structure-borne sensors along with the associated analysis equipment is now available on the market. There are also diagnostic systems for mechanical seals and bearings, and self-monitoring functions are built into in control systems.
Traditional sensors capture a value and then trigger something that no operator wants to see, namely a fault warning. Early warning systems kick in earlier, signaling a problem before the pump fails or is damaged.
Sophisticated monitoring systems make sense on large pumps. By monitoring vibration levels, current and voltage fluctuations and changes in process parameters (temperature, pressure and flow rate), these systems are capable of providing dependable early warning about potential problems caused by out-of-spec operation or wear.
However, nobody winds up in the emergency room just because they catch a minor cold. The cost and effort invested in monitoring must be commensurate with the risk and the value of the pump. Not all pumps are equally important. It is not always a big problem if a secondary piece of equipment fails unexpectedly. The next level down is component monitoring, which means keeping an eye on diaphragms, valves, cans and bearings. Experts only recommend the use of intelligent early warning systems when this level of sophistication is actually warranted.
It is generally accepted that structure-borne noise is a reliable indicator of faults on rotating parts. The only problem with sensors is the financial aspect. The crucial issue is criteria extraction. How and when does the operator recognize that there is a problem? The goal is to associate a unique frequency with each fault. This approach already works for functional components in the oscillating pump head of diaphragm pumps. These condition monitoring systems detect the majority of possible faults, for example a leaky fluid valve (these highly sensitive systems monitor the timing between the structure-based noise signal and the intake and pressure stroke). It is now possible to reliably detect leakage greater than 1 %. The combined analysis of structure-based noise and pressure signals leads to a detection of 90 % of possible failures according to the provider.
When you are weighing up the pros and cons of intelligent early warning systems from the cost point of view, you should keep in mind that when you use these systems, service intervals always increase and the payback period is usually relatively short. You frequently hear that the cost of a monitoring system should not exceed 10 % of the value of the pump, but you should keep an open mind on this. How critical the system is to the customer is more important than the cost ratio between the monitoring solution and the pump.
Redundancy: the pros and cons of backup pumps
Redundant pumps are often used in the chemical industry to guarantee system availability (A and B pumps). The added cost inevitably leads people to ask where and under what conditions redundant pumps can be eliminated. Actually, there is no simple solution to this dilemma. When an operator is considering doing without a backup for a pump which runs continuously, the cost of starting up and shutting down the system and the cost of lost production resulting from a fault has to be compared to the additional cost of a backup pump.
The operator and the supplier take on a lot of responsibility if the decision is made not to use a backup. The product will have to meet very high quality standards, and the pump specification will have to be much more precise. Monitoring and early warning systems are essential in these applications. Experts advise operators to run the pump in the process which will be used later on to ensure that the specifications are correct. Verifying the process suitability of the pump during the commissioning phase gives the operator the opportunity to upgrade the pump, and the supplier has the chance to make improvements.
Quality assurance is particularly important when the pump is expensive and the lead time is very long. When you look at quality, you have to look at the quality of the pump itself, the quality of the process data and the quality of machine diagnostic/early warning systems. Process and specification data must be reliable and reproducible in order to make sure that the pump operates faultlessly.
Careful attention must be paid to the pump housing production process at the foundry or forge. It is not uncommon for operators to complain about substandard casting quality. Outsourcing of castings in low-cost countries was not and is not always accompanied by a suitable supplier qualification process. Is this the price we have to pay for globalization? Pump producers who have a problem need to act quickly.
Sealless pumps with no shaft seals: a 200 million euro market
Operators have to use pumps which have elaborate mechanical seals or pumps without shaft seals (magdrive or canned motor pumps) to safely handle dangerous or environmentally hazardous media and avoid the release of emissions.
Operators have the following options to eliminate the risk of leakage:
- hermetically-sealed pumps with canned motor drive (absolutely leakproof primary and secondary fluid containment, no buffer medium required)
- magdrive pumps (single casing, secondary mechanical seal needs to be monitored; buffer fluid must be reprocessed)
- multiple mechanical seal pumps with buffer fluid (buffer fluid must be reprocessed)
- multiple mechanical seal pumps with dry-running seal (buffer fluid must be reprocessed)
The crucial difference between canned motor drive and magdrive is the fact that the canned motor has secondary fluid containment. The terminal box and the cable glands have to be impermeable to gas and fluids, and they must be designed for the rated pressure of the subsystem. In case the can is destroyed as a result of bearing damage or corrosion, no hazardous substances can be released into the atmosphere. Magdrive pumps can be a safety hazard if a fault occurs. A double-wall can minimizes the risk to a large extent, but the space between the walls must be constantly monitored.
How large is the market for sealless pumps (canned motor drive and magdrive pumps)? The industry assumes that worldwide demand is in the region of € 200 million. The European market is estimated at € 60 million, and € 20 million of that is in Germany. The ratio of magdrive to canned motor drive is about 2:1.
Following the introduction of ATEX 100a which also applies to non-electric pumps, the ratio is expected to shift in favor of canned motor pumps. To comply with the new regulations, standard pumps (including magdrive pumps) require more monitoring to detect dry running and excessive temperature. Canned motor drives are electrical devices which already have appropriate safety features which make them inherently ATEX 100 compliant. Pump producers will present a large range of new and enhanced sealless pumps at ACHEMA 2006.
Metering pumps: migrating to system solutions
There are very few industrial applications where a centrifugal pump is inherently a bad choice. However, metering pumps are one example where this is in fact the case. Positive displacement pumps are the most popular solution in these applications. Manufacturers are obviously now paying more attention to the peripherals. A look at current products on the market reveals a move towards system solutions. The main advantages are one-stop shopping with a single point of contact, elimination of interfacing problems between the components and elimination of assembly work. The turn-key systems are supplied fully assembled. On request, the system can be installed and commissioned on site. This removes most potential sources of error.
The market seems to be ready to embrace individual modules. The reason for this is that the properties of the medium and the degree of precision needed for the process are important criteria in any given application. Even metering applications which appear to be simple always have a holistic aspect, making a system approach superior to installation of separate components.
Fittings: driving down the cost of automation
German producers of industrial fittings were able to increase turnover by 7 % (+13 % in the export sector) in the first half of 2005. There were significant differences between the various product segments. Turnover of shut-off valves showed the strongest growth at 10 % (+4 % in the domestic market and +18 % in the export markets). Safety and monitoring equipment was up 5 % (domestic: -5 %; export: +16 %). Domestic and foreign turnover in the control valve segment grew by a modest 2 %.
Despite the fact that demand for control valves was down in the period, the percentage of automated valves and fittings continues to increase.
Two types of requirements profiles are common in automation applications. Some valves operate purely in on-off mode, and the valve is only moved to one of the end positions. In control mode, the flow rate in a pipe is monitored to detect deviations from a setpoint. When you are looking at automation costs, there is more involved than just the choice of the fittings themselves. The type of actuator (manual, electrical, pneumatic or hydraulic) also influences the cost of the automation project. Various combinations produce different mixes of investment, operating and energy costs. Visitors to ACHEMA 2006 will have the opportunity to review the products and solutions which are on offer from a range of valve and fitting suppliers.
Compared to linear controls (valves and sliders), it takes less force to operate 90° controls (flaps and stop-cocks), so the actuators can be small and cheaper.
Here is a practical example, which shows what “cheaper” can mean. In October 2005, a technical fault interrupted production in a steam cracker at a large chemical plant. The safety systems reacted as intended, and the raw gas was burned off at the flare. The cause of the problem was traced to “atypical mechanical damage to the actuator” on a special valve, and the resulting costs were enormous. For every hour that the flare burned at the steam cracker, the company lost tens of thousands of euros, and it took several hours before the flare went out. This is a typical example of how a relatively “cheap” component can cause enormous damage.
One topic will certainly be on the minds of producers and users at ACHEMA 2006. All industrial plants in Germany will have to comply with the European regulations (IPPC Directive 96/61/EC) and national legislation (air quality, etc.) by 2007. This affects valve spindle and housing seals. Successful implementation depends on the quality of the sealing components and on the state of existing valves (rework may be necessary). It is also important that the seals are properly installed. Additional measures, for example using disk springs on the gland, provide an additional margin of safety in difficult spindle sealing applications. The incremental cost associated with compliance to the regulations is not without its benefits, however. Correct planning and implementation increase service life and maintenance intervals.
The trend to unit-based solutions is also evident in the valve industry, for example pressure reducers and temperature control stations. For users and plant engineers, the number of components which need to be sourced is reduced substantially when subsystems are available. The supplier takes responsibility for detailed design of valves, fittings, pipes, etc. which are installed in the unit and which must comply with applicable regulations and standards. The supplier also takes care of certification and provides a complete set of documentation.
The potential advantages to operators, who take an in-depth look at life cycle costs when they evaluate pumps and fittings, go beyond a possible reduction in energy costs. Lower life cycle costs provide an indication that the pumps or fittings are compatible with the system and the process and that they are less likely to fail. Sometimes it is necessary to look at alternatives, and a recently published study claims that there are cases where a new solution can be a good investment. A life cycle analysis provides a good basis for comparing different pump designs, and there can be considerable differences. On the other hand, life cycle costs are unlikely to vary significantly on pumps with similar designs which are made by different manufacturers.
More than 850 companies will showcase their latest technology and their proven designs in Halls 8 and 9 at this year’s ACHEMA.
Source: DECHEMA Ausstellungs-GmbH