BWT’s New Pharmaceutical Water System Makes Drug Manufacturing Safer
Water is the most important raw material in the manufacture of drugs, vaccines and cosmetics. The new Loopo pharma water distribution system, developed by BWT Pharma & Biotech, provides the highest standard of hygiene safety in the treatment of pure water, highly purified water (PW/HPW) and water for injection (WFI).
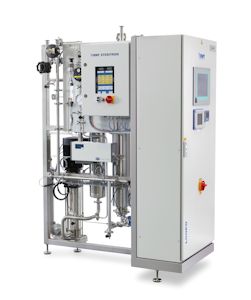
New pharmaceutical water system Loopo (Image: BWT)
Pharmaceutical water produced from drinking water is a source material and excipient for pharmaceutical and biotechnology industry products such as cleaning and rinsing agents, for which statutory minimum physiochemical and microbiological standards apply, as specified by national pharmacopoeias and monographs (e.g. European pharmacopoeia, EP and US Pharmacopoeia, USP).
BWT Pharma & Biotech is a leading European provider of innovative, turnkey full-service systems for clients in the pharmaceutical and cosmetic industry. Following the launch of its new generation Osmotron/ Osmovision pharma water system, BWT Pharma & Biotech has now developed further the Loopo system range, setting new standards of hygiene and operational efficiency for the process used for the storage and distribution of supply media, where quality cannot be compromised.
BWT Loopo is a compact, standardised system for the distribution, sanitisation, control and monitoring of purified and highly purified water or water-for-injection circulation systems. It offers a reliable and safe means of maintaining the quality benchmarks achieved in the water treatment process throughout the production process chain, right up to the finished product. The combination of innovative BWT technologies and processes provides a particularly high standard of hygiene, coupled with low operating costs and environmental benefits.
Two types of BWT Loopo are available: cold water (LoopoO C), for purified and highly purified water (PW/HPW), and hot water (Loopo H) for water for injection (WFI), plus four standard capacities of 3,000-23,000 litres per hour. Larger capacities for specific projects can also be accommodated using the same concept.
In the Loopo C variant, the storage tank, the area most vulnerable to germs, receives a constant supply of ozonated water from the integrated BWT Steritron ozone generation system for the prevention of microbial growth. The excess of any residual ozone is then reduced to below the detection limit of 5ppb upstream of the tapping points using BWT Bewades UV disinfection. This avoids extensive, costly sanitisation and sterlisation of the distribution systems and eliminates the need for increased investment in total isolation.
All the systems are fully pre-tested and certified, and their ultra compact design means that they can be easily integrated into existing systems. BWT Aqu@View’s certified, totally automated controls, with full graphic display, make the systems very easy to operate. Using calibrated, high-quality measuring systems for TOC, conductivity, ozone, pressure, temperature and flow, all the relevant process data is archived securely and clearly on a tamper-resistant data recorder. All the data can then be safely transferred from the controls to the master control system via certified data blocks. Large distribution systems with several hundred tapping points can also be fully controlled and supplied via an intelligent priority control system.
Source: BWT Wassertechnik GmbH