BioChop®Hygienisation
EC-regulation No. 1774/2002 of October 3rd 2002 on health rules concerning animal by-products not intended for human consumption, also known as the by-product regulation, now opens the way for new possibilities for companies producing varying quantities of animal by-products.
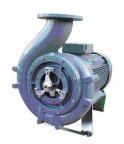
Landia BioChop chopper pump (photo: Landia A/S)
The by-product-regulation allows the use of category 3 animal by-products at biogas plants, provided that these products have been pasteurised or sanitised at 70º C for at least one hour and that the size of the solid parts does not exceed 12 mm.
It is an accepted fact that in order to obtain a cost-effective operation of biogas plants a catalyzer in the form of organic waste or by-products must aid the process. Typically, these by-products originate from the food industry, such as abattoirs or fish and poultry processing companies.
Landia has been abreast of this development and now offers the BioChop hygienisation unit. The first unit is already in operation at the Rybjerg Biogas plant.
The Rybjerg project
At the municipal wastewater treatment plant a flotation plant processes all wastewater from the nearby fish industry. The flotation plant separates the wastewater in two; a liquid part which is pumped to the plant for treatment and a sludge part disposed of to the biogas plant. The flotation sludge is comprised by the new by-product regulation and must thus be hygienised at 70º C for an hour before it is led to the digester of the biogas plant.
The solution
A Landia BioChop hygienisation unit having a volume of 2.5 m3 is installed at the Rybjerg Biogas plant. The capacity depends on the present heat quantity; the average capacity lies between 20 and 25 tonnes a day at continuous operation.
The BioChop hygienisation unit is characterised by its simple design with operationally reliable high-quality components. The tank, the pipe, the heat shield and the valves are made of stainless steel. The unique design of the unit makes it possible to chop solid parts, to mix and to empty the tank after the hygienisation process by using only one pump, i.e. a Landia BioChop chopper pump.
Control system
The hygienisation unit includes a PLC-control developed by Landia, which regulates all phases of the hygienisation process. Landia have integrated a data logger as part of the control. This is a data collector whose task it is to register the hygienisation time and the temperature. Since the plant has been approved by the authorities, naturally, it must be verified that the requirements of 70º C for 1 hour are met.
This is how it works
At the Rybjerg Biogas plant the hygienisation unit has become an integral part of the biogas plant.
The flotation sludge from the treatment plant is kept in the reception tank prior to the hygienisation process. The bottom of the reception tank is equipped with heating coils – even during the coldest winter the sludge temperature will not fall below 10 – 15º C.
The flotation sludge is pumped from the reception tank to the hygienisation unit. A return pipe connects the two tanks. In case of excess pumping or foaming from the heated sludge a contamination of the surrounding area will thus be avoided.
After the heating and hygienisation process the BioChop pump will pump the substrate directly from the hygienisation unit to the digester.
Numerous possibilities
At the Rybjerg Biogas plant the hygienisation unit has been placed at the biogas plant itself. It is, however, possible to place the unit at the factories where the animal by-products are produced. In many situations the hygienisation unit will contribute to a simpler and improved hygienic handling of the by-product, since the substrate – apart from being heat-treated – is made pumpable in a closed system. This means that the substrate can be pumped to a storage tank or directly to a tank lorry, thus avoiding e.g. open containers.
Advantages
The hygienisation unit is characterised by its simple design. The material and the main components are high quality - the entire BioChop tank is made of stainless steel and thus provides maximum protection against corrosion.
There are absolutely no moving parts inside the BioChop tank. Thus it will never be necessary to enter the tank to carry out maintenance. Actually, the maintenance costs will be at a minimum since the only component at the BioChop hygienisation unit that will require regular maintenance is the BioChop pump.
Among several others, one of the positive side effects is the heat-treatment of the hygienised substrate. In fact, the plant can function as a heat exchanger. Furthermore, the heated substrate is easily pumpable, and the chopping to a particle size less than 12 mm ensures the optimum use in the biogas plant reactor tank, thus resulting in an increased gas production.
About Landia
Landia A/S provides solutions for the handling of difficult liquids within e.g. biogas production, municipal and industrial wastewater treatment, food industry and agriculture. For these applications Landia is a market leader.
Source: Landia a/s