Best Practice in Pumps for WFI Systems
Used in final formulation in the pharmaceutical industry, it is absolutely essential that water for injection (WFI) maintains its sterile condition. This is why the WFI system – and in particular the pump – must be carefully designed to deal with the demanding physical properties of pure water.
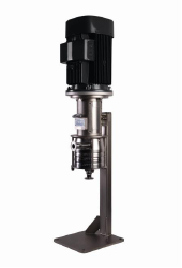
Fully drainable pump (Photo: Grundfos)
Equally important, the pumps must be able to cope efficiently with the required flow and pressure and ensure that the sterility of the water is not jeopardised. The European, the Japanese and the US pharmacopoeia may differ slightly from one another but the pump challenges encountered in WFI productions are essentially the same. And so are the benefits of going for the optimum pump solution.
The optimal pump material
With the conductivity typically below 1.5 microS/cm and the pH value between 5-7 the physical properties of WFI place great demand on the pump material. The water finds itself in a state of unstability and in trying to regain its natural status the media becomes highly aggressive to the material it is in contact with – even to high grade stainless steel, which is the preferred material of construction for all wetted pump components in WFI systems. For this reason the recommended type of stainless steel is AISI 316L with a ferrite content less than 1%. As for the surface finish the roughness must be less than 0.5 ųm in order to reduce the risk of microbial growth.
The robust shaft seal
The shaft seal is one of the most critical components in terms of the pump s operational reliability in WFI systems. As a barrier between the pumped liquid and the surrounding environment, the shaft seal plays an important part in eliminating any risk of contamination of the sterile water – and in preventing leakage. In choosing the optimum shaft seal solution in WFI pumps the following critical aspects must be taken into account:
- Exposure to an “aggressive” liquid (WFI)
- Exposure to high temperature water (typically 80°C)
The optimum choice in material for shaft seals exposed to WFI is silicium carbide. Silicium carbide is a highly abrasion-resistant, chemical inactive and durable material, which is approved for shaft seals in pharmaceutical applications. Carbon/stainless steel shaft seals are unsuitable as carbon abrasion could interfere with the sterile status of the WFI.
The most challenging aspect of shaft seal operation in WFI systems is the fact that the purity and the relatively high temperature of the liquid combined cause poorer lubrication of the seal faces. This may induce noisy friction and wears heavily on the shaft seal, reducing the life of this essential component. In this respect, choosing a pump with a double shaft seal is the optimum solution. A flushed double shaft seal with seal water offers the following advantages:
- Improved lubrication
- Better protection against dry running
- Efficient cooling of the shaft seal
- Increased operational safety by further safeguarding against contamination
- Significantly increased lifetime of the shaft seal.
The initial cost of a pump with a double shaft seal is obviously higher and so are the operational costs due to the consumption of cooling water for seal flush (typically 4-5 l/hrs. However, the value of the above-mentioned advantages often more than compensates for the difference because costly system downtime can be avoided. So a double shaft seal solution may prove to have a positive impact on the reliability of the entire WFI production system.
The essential drainability
WFI systems invariably demand that pumps are fully drainable to ensure a reliable SIP (Sterilisation In Place) operation. Vertically installed aseptic pumps offer unmatched drainability and high operational safety compared to traditional pump systems.
Where traditional horizontal pumps must be fitted with separate drain valves, which add a dead leg on the casing, the self draining vertical pump has been designed without these potential sources of risk, allowing for a much safer production of WFI. The fewer hideaways bacteria are given, the less likely is the occurrence of contamination of the sterile water.
In addition to optimising the performance of the WFI system the vertical pump is literally ready for installation straight from the factory because it does not require added costly components, e.g. valve and valve control.
The beneficial control
Water for injection must be constantly circulated in the distribution loop in order to maintain its sterile properties. This places great demand on the pump in terms of maintaining the correct pressure and flow at all times – even when water is being drawn from the system in large amounts at one go. This can either be done by operating the pump at constant full speed or – preferably – by adjusting the speed according to the required flow by means of variable speed control.
The use of pump control is considered best practice in WFI systems as it offers a number of benefits:
- Reduced energy consumption
- Optimised system performance
- Increased comfort (e.g. less noise)
Today, pumps can be equipped with integrated frequency drives to ensure an optimum match between the frequency drive parameters and the actual pump requirements. This further reduces the time for parameter setting and significantly minimises the risk of incorrect settings. Moreover, if the pump features external couplings between the motor and the pump shaft, the frequency drive and the motor can very quickly be replaced in case of maintenance – without having to re-sterilise the WFI system.
The required documentation
In WFI systems, it is recommended to only ever choose pumps that have been certified according to the EHEDG standard for cleanability (CIP) and sterilisability (SIP). The EHEDG standard guarantees that the fundamental design of the pump has been tested in a standardised way.
All wetted metal parts of the pump must be delivered with material traceability certificates (EN 3.1.) and all non-metal parts must be delivered with a FDA conformity declaration. This is to make sure that the delivered pump actually contains the correct materials for safe operation – and to ensure proper documentation for the final validation of the entire WFI system.
To summarise, the optimum pump solution for WFI systems carefully considers design and performance in relation to the demanding environment it must operate in. An optimised solution will be beneficial to the entire WFI system and optimise operational reliability as well as product safety.
Source: Grundfos Holding A/S