AxFlow Give 70-Year Old Drysdale Pumps a New Lease of Life
Few people will have forgotten the massive flooding in the Doncaster area on 25th June 2007 when around 80mm of rain fell in a 16 hour period. Amongst the many domestic and commercial casualties was the Bentley Ings pumping station which suffered a power failure.
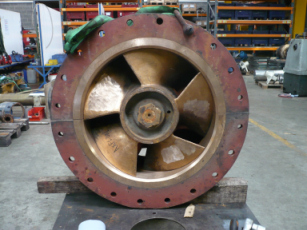
The first of Drysdale pumps fitted with a new wear ring
The switchgear ended up submerged in water so the pumps, which had provided many years of reliable service, stopped operating.
In response to this event, the pumping station’s owners British Coal, through the Environment Agency, have instigated an enlightened programme of works to restore the pumping station to full operating capacity and enhanced efficiency. The switchgear has now been repositioned to a higher level and the pumps are undergoing a major refurbishment programme which will result in many more years of reliable operation.
The refurbishment and retrofitting of the three Drysdale 24-inch vertical axial flow land drainage pumps and one dry weather pump incapacitated by the flood waters was awarded to AxFlow Limited by the Environment Agency’s contractor AMCO.
“The first task was to remove the pumps from the site and transport them to our Huddersfield site,” reports Mark Redgrove at AxFlow. “Once we had the pumps back in our Huddersfield workshops and stripped down we were able to assess their condition and recommend to AMCO what work needed to be carried out. Because of their continued operation and performance under the ever-watchful eye of the EA, it had not been necessary to take Drysdale water drainage pumps out of service for more than 20 years. Close inspection revealed that the pumps were almost 70 years old and it was only because of their original build quality and management by the EA that they had continued to operate. However, it was inevitable that after all this time there was evidence of component wear.”
In a situation such as this, the course of action often followed is either to go to the equipment manufacturer for remedial work or to purchase completely new pumps. Unfortunately, the first route was not an option as the manufacturer had long ceased to exist. The second course of action had to be considered, but on the advice of AxFlow’s engineers AMCO and the EA considered that this would not produce the best value for money over the long term.
Given the age of the first two pumps to be inspected, AxFlow could see that the job of giving the pumps a new lease of life and improving their efficiency would be a challenge. AxFlow also found that the dry weather or ‘summer’ pump had a smaller intake diameter than that of the discharge, a factor often associated with problems of cavitation, but easily remedied by throttling-off the intake.
“Whilst both the two Drysdale pumps displayed performance wear, it was the No.3 pump that gave us the most concern,” says Mark Redgrove. “The motor was in good shape, although heavily contaminated internally with grease, and several major components required repair or replacement. The Michell bearing journal pads were badly scored and required re-metalling and finishing. Plus there was a large amount of white metal loose in the bearing housing. The line shaft bearings were badly worn and the wear on the corresponding shaft bearings meant that these had to be rebuilt to the original diameter.”
Looking at the pump end components, the impeller bush cap was found to have sheared its studs and was loose inside the pump. Consequently, the bearing and cap was badly worn. “Because the bearing cap and bearing were both worn and no longer concentric to the top bearing, we proposed line boring the casing to true-up the bore before fitting an oversized bearing bush,” says Mark Redgrove. “As a result of the bearing being loose, the impeller/shaft had been allowed to run-out far more than it should, causing wear between the impeller and wear-ring. To rectify this we recommended replacement of the wear-ring. In addition, because of the excessive wear on the impeller, our advice was to braze replacement tips on each vane and then machine them back to the original diameter. Finally, we would shot blast the casing components, paint the internals with Bitumen and, as with the No.2 pump, we would replace the gland packing.”
The No.2 pump required much of the same attention and work, but it was the clearance between the impeller and the wear-ring that caused concern. When measured, the clearance measured 7.8mm on diameter, whereas the recommended clearance for this size of pump is typically around 0.9mm on diameter. To rectify this, AxFlow replaced the wear-ring, this action returning the clearance to the original diameter. AxFlow’s engineers also found that the pump end bearing was missing a sleeve, leaving a clearance of 3mm between the bearing and the shaft journal. This problem was solved by rebuilding the shaft journal and re-metalling the bearing.
The work undertaken by AxFlow addressed the engineering issues that would get the drainage pumps at Bentley Ings back into service and ensure a long and reliable working life. Even though the pumps were of a considerable age and no longer in manufacture, AxFlow showed that it had the mechanical engineering resources and pump knowledge to repair the pumps and to ensure that once repaired and installed they would give an improved and more efficient operation.
By accepting the findings of AxFlow’s examination of the pumps and what work would have to be undertaken not just to put them back into service, but also to optimise performance, the EA has ensured a sound and economical future for the pumping station for the coming 20- 30 years.
Source: AxFlow Group