Armstrong Launches New Integrated Packaged Pump Solution
Armstrong has announced the launch of a new generation of integrated, pre-designed packaged pump solutions which deliver lowest first installed cost, reduced project risk and outstanding energy efficiency performance.
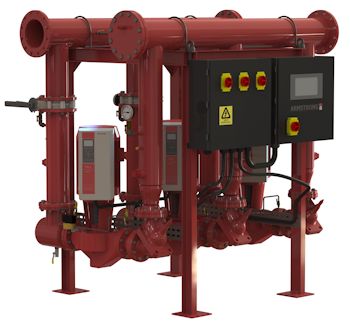
The new Armstrong iFMS integrated, pre-designed packaged pump solution.
Building on the success of the Armstrong 8000 Series of pump packages, the new iFMS (Integrated Fluid Management Systems) have the added benefit of offering outstanding energy efficient performance across a wider operating envelope than ever before. Designed with a built-in safety net, they continue to optimise the energy efficiency of the installation even if operational requirements change, either during the design process or after installation, without the risk of underperformance or the need for replacement.
The iFMS is a complete fluid management system, pre-designed and pre-assembled by Armstrong, which can be configured to suit the widest range of applications. Costs involved in designing the system are removed, and as the pump solutions are designed by Armstrong (a world-leading manufacturer of HVAC equipment with almost 80 years experience in pump design) they offer the best possible integration of pumps with controls technology for exceptional performance.
In addition, as the pump package is fully assembled and tested before it leaves Armstrong’s factory, many potential project risks are eliminated. Poor system integration during installation is avoided, and the pump solution can be manufactured concurrently with other parts of the construction or refurbishment project to reduce the schedule significantly, at the same time as avoiding delays or bottle-necks that might occur on-site. These factors combine to offer specifiers a high-performance product solution, at the lowest first installed cost, with reduced risk and shorter installation times.
An additional advantage of the iFMS is that it features Armstrong’s innovative Design Envelope variable speed, demand based pump control, which enables it to optimise energy efficiency capabilities over a wider operational range. Changes to spec are common during the design phase of a project, involving consultants and other engineers in costly re-designs. The wider scope of requirements covered by the iFMS packaged pump solution, however, can reduce iterations of pump selection, reducing levels of risk and safeguarding profit margins across the supply chain. In addition, after installation, the iFMS’s wider capabilities can accommodate variations in requirements resulting from increased occupant density, alterations of building design, or changes to building use. For building owners this can bring greater adaptability without costly HVAC refurbishment, at the same time as ensuring continued optimisation of pump efficiency.
The performance envelopes are mapped to enable the most efficient pumps to be selected for 50% of the design flow rate, where variable flow systems operate most often. This ensures a building’s hydronic pumping system consumes as little energy as possible. In addition to ensuring that the installation is compliant with 2017 legislation on pump motor efficiency, the in-built intelligence delivers energy savings of up to 70%, reducing carbon impact in excess of current legal requirements, and reducing costs, to deliver even greater benefit to building occupiers and owners.
In addition to these benefits, the iFMS offers valuable installation savings. Equipped with Armstrong’s Sensorless design feature, the pump packages do not require external sensors to monitor and control the HVAC load, removing the additional cost and technical complexity of installing Variable Frequency Drives.
Installation cost savings are also provided by Armstrong Suction Guides and Flo-Trex valves, which reduce the requirement for pipework and fittings, and perform multiple functions with a single component. This speeds up installation and reduces cost at the same time as offering a valuable reduction in physical footprint.
Finally, the iFMS reduces project risk significantly by providing a single source of responsibility for the entire process of design, procurement, supply, installation, commissioning, service and maintenance. In addition to being a technically-superior approach to equipment supply, this offers significant commercial advantages by offering a shorter, simplified and more robust supply chain for any project.