Allweiler Pumps in Exhaust Gas Treatment Systems in Ships
As environmental regulations become more stringent, waste gas treatment systems are growing in importance. H+H Umwelt- und Industrietechnik GmbH of central Germany has been using Allweiler progressing cavity pumps as a core component of these systems since 2003.
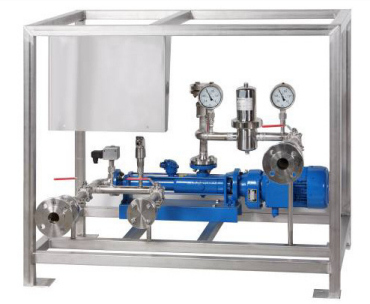
Allweiler progressing cavity pumps of the "ANBP” and “AEB” series in block design are used in the pump stations.
The company has been manufacturing catalytic waste gas treatment systems since 1998. Originally they focused on applications in block heating stations and industrial plants. But stricter environmental regulations introduced in Scandinavia and in the Baltic Sea in 2004 have boosted demand for shipborne systems. Introduction of a NOx tax in Norway has further increased demand. NOx-reduction systems are used on ships for the propulsion system’s heavy oil motor and for auxiliary equipment like power generators. The first of these systems produced by H+H was commissioned in 2005. Since 2004, the company has been the global market leader for maritime Selective Catalytic Reduction systems (SCR) with a market share of approximately 80%. Currently about 600 of these single systems, known by the name “EcoMarin”, are operational on 160 ships.
Pulsation-free Pumping
Progressing cavity pumps from Allweiler AG, a Colfax business unit, play a major role in the finished products. These pumps feed urea to the SCR system’s dosing panels. The urea is heated to a high temperature in the waste gas. The resulting ammonia serves as a reducing agent in the system. Due to the difficulty of storing ammonia, it is not possible to simply keep the material onboard the ship in "ready-to-use" form.
Allweiler pumps continuously circulate urea in a closed loop; excessive amounts of the material are fed back into the tank. A major advantage of these pumps is their pulsation-free pumping characteristics. Even when starting, they do not produce pressure surges that could damage the system.
Rapid Delivery
Allweiler’s tremendous flexibility and ability to react quickly to individual requirements were key factors in H+H’s decision to use Allweiler for these critical components. Speed and flexibility are particularly important for shipborne systems. For example, power supplies on ships can vary between 230 and 690 V, so having the right pump motor is very important. In many cases, H+H has only eight to ten weeks from the time an order is placed until the system is delivered, so fast reactions and direct contact with the supplier are essential. The pumped liquids (32% to 40% urea and 12% to 24% ammonia water) are very demanding on the pump materials. Allweiler manufactures its own stators and can choose the best possible combination from 20 different materials. Other parts that contact the pumped liquid directly, such as the joint collar, are also made of specially adapted materials to give them an extended service life. Pump casings are made of stainless steel. These configurations allow the pumps to achieve continuous operating times of 8000 hours or more.
The pumps operate continuously instead of being controlled by frequency converters. Frequency converter controls have proven to be too sensitive and complex for practical applications. They also influence the ship’s power supply network. In this configuration and installation, the systems and pumps even meet the high requirements of military applications and have already been installed in several naval vessels.
Source: ALLWEILER GmbH