Triplex Process Diaphragm Pumps Reliably Convey Critical Medium
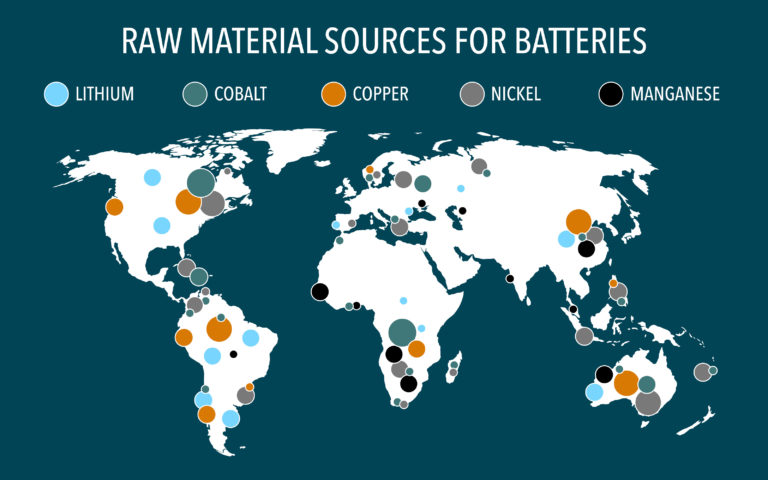
The valuable raw material, which is needed for battery technologies and therefore plays a central role in the energy transition, is mined mainly in Indonesia, but also, for example, in the Ramu Nickel Cobalt Project near Madang on Papua New Guinea. (Image source: Adobe Stock)
The decision was made in favor of particularly robust LEWA triplex pumps of the type G3G, which feature the proven LEWA diaphragm technology and ensure safe and reliable operation despite the difficult medium. They are equipped with hermetically tight M500 pump heads with a hydraulically actuated PTFE diaphragm, suitable for discharge pressures up to 350 bar. The pump heads are designed to be drained. What's more, the durable overall design is based on a one-piece crankcase and double-bearing crankshaft. For five years, the LEWA process diaphragm pumps have been operating successfully in Papua New Guinea. Therefore, the problem-prone predecessor models have been replaced by triplex G3G pumps as well at two other sites in Indonesia some months ago.
"We assume that – depending on the scenario –, global nickel demand will increase from around 2.4 million tons today to around 3.4 million tons in 2025," said Dr. Michael Szurlies, nickel expert at the German Federal Institute for Geosciences and Natural Resources (BGR) in the summer of 2021. The valuable raw material, which is needed for battery technologies and therefore plays a central role in the energy transition, is mined mainly in Indonesia, but also, for example, in the Ramu Nickel Cobalt Project near Madang on Papua New Guinea. The nickel/cobalt intermediate produced there yields a total of 31,000 t of nickel metal and 3,000 t of cobalt per year.
Pumps susceptible to failure in the HPAL process
The ore is processed there using the high pressure acid leaching (HPAL) process. In this process, nickel laterite reacts with sulfuric acid in the autoclave. Nickel in the form of sulfate is leached out at a high temperature and high pressure, while iron in the form of hematite enters the leached residue. Washing and thickening precipitate the leach solution with hydrogen sulfide, magnesium or sodium hydroxide to produce an intermediate nickel-cobalt sulfide or nickel-cobalt hydroxides. By leaching, extraction and electrolytic recovery, this product can be used to produce stainless steels such as Hastelloy.
As part of this process, 30 m3 of 98-percent sulfuric acid per hour must be meterd into a high-pressure reaction vessel at a pressure of 70 bar. "For this task, the mine operator initially had cost-optimized pumps from a regional manufacturer," explained Toni Zhong, Marketing & Business Development Manager at LEWA NIKKISO (Dalian) Fluid Technology Co., Ltd. "However, these pumps operated at very irregular intervals and had a high failure rate." Downtimes were also very long, for example, when the crankshaft in the drive unit had to be replaced. Those responsible therefore decided to replace the units and purchase new models that more reliably convey the difficult, corrosive medium.
Durable new aggregates with low maintenance requirements
Due to their robustness, durability and hermetic tightness, the decision was made in favor of G3G triplex process diaphragm pumps with the M500 pump head from LEWA. "Like all triplex pumps, the G3G is designed for continuous operation to ensure long-term uninterrupted and trouble-free operation," Zhong said. Durability is achieved in particular by the drive element housing, which is a one-piece design with a vertically flanged engine, and by the double-bearing crank shaft. In addition, the mono-block design ensures that the required components such as bearings and gaskets could be reduced to an absolute minimum, resulting in an extremely compact, space-saving design. The flow rate can be controlled using a frequency inverter that regulates the change of the engine RPM, the number of strokes per minute and thus the flow rate. Because all components are designed for continuous stress, trouble-free operation for more than 40,000 h is possible with the drive unit.
The M500 pump head with hydraulically actuated sandwich diaphragm made of pure PTFE is designed for discharge pressures up to 350 bar or flow rates up to 19 m³/h, and is protected against operating errors and impermissible operating states. For example, an integrated, individually adjustable pressure relief valve in the hydraulic part prevents possible overload situations during operation. In addition, the patented DPS protection system and the diaphragm monitoring system report any damage to the diaphragm in good time before it ruptures and the metered liquid can escape into the environment. "Even in case of massive failure, the DPS ensures that the pump remains stable and hermetically tight so that it can be safely started up from any operating state," Zhong said. "This minimizes the risk of sulfuric acid leaks and the risk of accidents." In addition, the maintenance requirements for these units are very low because the metered liquids do not come into contact with rotating components. This is due to the fact that all moving parts operate in a protective and lubricating hydraulic fluid. Other features of the triplex pumps for this application are the newly developed cone valves with valve seats and plugs made of Hastelloy. These ensure trouble-free continuous operation. In addition, the pumps are characterized by their smooth running and a low-pulsation flow rate, often rendering pulsation dampeners superfluous. This makes them ideally suited for use in the HPAL process.
Minimized downtime
The aggregates have been in operation for five years at the Ramu Mine in Papua New Guinea and for twelve months at the Legions and the Huayue Nickel Cobalt Projects in Indonesia. Since then, failures and downtime have been significantly reduced compared to previous models. "The customer is very satisfied with the projects with LEWA NIKKISO and plans further cooperation in similar applications," Zhong said in summary.
Source: LEWA GmbH