25 Years of Gemü Multi-port Valve Blocks
The valve specialist based in Ingelfingen is celebrating its 25th anniversary with high-quality multi-port valve blocks (M blocks) in stainless steel.
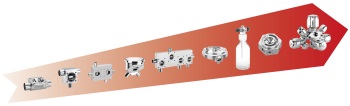
Evolution of diaphragm valves – 25 years of M blocks (Image: Gemü)
Originally, a pipeline construction consisted of welding simple investment cast or 2/2-way valve bodies together with pipe fittings. And these are to some extent still used today, but they have a substantial disadvantage due to the large deadlegs. It was for this reason that the first simple multi-port valve body was made in 1993 – the T valve, which was self-draining and featured integrated pipe fittings without any weld seams at all. Nowadays, the M blocks are the most advanced solution for dealing with the high, complex plant engineering requirements of the pharmaceutical, biotechnological, chemical and foodstuff industry.
Unlike the time-consuming welding configurations, M blocks are manufactured entirely in stainless steel block material. As a result, they have a compact and multi-functional design, greatly reduced deadlegs, a reduced hold-up volume and improved protection of expertise for plant operators. Furthermore, product reliability is increased since there is no need for any weld seams. In addition to all current connection standards, even special process connection such as Tri-Clamps or hygienically compatible seal contours can be incorporated directly into the valve bodies. The experienced developers at Gemü know virtually no limits when it comes to the customized design of the M blocks. More than 1200 different designs with over 25,000 specific customer solutions in a wide range of stainless steel alloys have already been implemented.
In addition to the classic M block with diaphragm valve seats, various shut-off concepts and sealing principles such as globe valves and the award-winning Gemü PD design can also be combined. Plastic M block solutions are also available in the standard version and their material properties mean that they can be used in semiconductor systems, for (waste) water treatment or in the chemical industry. The valve specialist is already concentrating on innovative manufacturing methods such as Laser Additive Manufacturing (3D printing) in order to support customers with expertise and innovative capacity both now and in the future.