Jung Process Systems Assembles Hyghspin Hopper with Double-acting Mechanical Seal
Enterprises of the chemical industry have versatile demands with regard to the technology of pumps. Specially in the sector of the Polymer chemistry the choice of adequate sealings is most important in order to guarantee failure-free conveyance of the products.
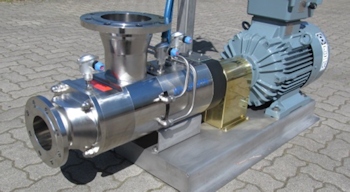
Hyghspin 90 with hopper for non-flowable media (Image: Jung Process Systems)
Jung Process Systems developed a special transport solution for a producer of inorganic adhesives on basis of Polymer using a Hyghspin Hopper with double-acting mechanical seal.
Transport of adhesives is viscous and sticky. The characteristics needed for the final product require tremendous challenges for the production technology. The product of the customer of Jung Process Systems has a viscosity of approx.100.000 mPas. Besides the high viscosity also the heavy friction losses in the piping at the suction side and a resulting very low NPSHa value demand sophisticated requirements regarding the pump to be used. Consequently the inflow of the product into the feed screw chamber is problematic. Due to these reasons the customer decided for the hopper execution of the Hyghspin twin screw pump series. However, contrary to the standard version this pump inlet is executed as a flange because the adhesive is processed in a closed circuit. A further feature represents the execution of the pump with a double-acting mechanical seal with pressurized buffer system instead of a lip sealing. Due to admission of the mechanical seal with a barrier liquid any kind of product outlet to the environment will be avoided just as the feed medium entry between the surfaces. This solution facilitates that the high-viscous feed medium falls into the feed chamber and can be transported pulsation-free and continuously without any problems.
3-in-1-Principle convinces
Product feeding, conveying and cleaning by means of the innovative construction of the Hyghspin Hopper twin screw pumps developed by Jung Process Systems. The feeding medium supply is effected in the extruder area underneath the feed hopper, the pressure increase is made in the proper pump area by means of the feed screws which are individually laid out for every particular application. This construction principle also convinced the producer of the adhesives. This manufacturer decided for a Hyghspin Hopper of design size 90. This pump accomplishes a differential pressure of 15 bar, the feeding quantity varies between 1 and 10 m3/h. The pump is located in an ATEX area 1.
Source: Jung Process Systems GmbH