Oil-Injected Screw Compressors Get Efficiency Boost
Atlas Copco Compressors has launched a new range of its GA 15-26 kW oil-injected screw compressors offering improved performance, reduced power consumption and lower noise levels. The redesigned range, which has been extended up to 26 kW, is built to be economical, reliable and efficient.
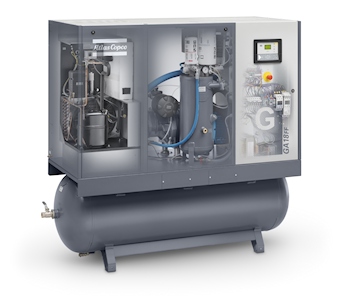
GA18 FF compressor (Image: Atlas Copco)
Compared to the previous GA 15-22 range, the new GA 15-26 models offer increased performance (Free Air Delivery up by 5%) and lower power consumption (Specific Energy Requirement down by 2%).
“For decades, our popular GA 15-22 range has been the perfect solution for workshops, installation companies and OEMs all over the world; and renowned for its reliability and low cost of ownership,” says Bert Derom, Vice-President Marketing. “With this redesign, we did not touch any of these benefits, we just made our GA even better by improving the drive train and cooling fan to boost efficiency and by extending the range to 26 kW.”
Major energy and performance improvements come from the GA’s improved drive train, which features an IE3 motor (NEMA Class 1) and a new, in-house designed compressor element. Compared to belt-driven variants, the gear-driven GA 15-26 offers a 3% increase in efficiency. Reduced pressure drops and improved cooling flow account for a further 2% performance increase, bringing the total Free Air Delivery gain up to 5% on average, across the complete range.
The GA 15-26 range also delivers more air at the same power consumption and does so in near-silence. The new drive train is more energy-efficient and features a new cooling fan that consumes less power and is quieter than its predecessor. Overall, the Specific Energy Requirement (SER) is improved by 2% on average. All of these new components have reduced the sound level of the compressors to as low as 65 dB(A), making a major difference when the unit is close to the point of use.
The GA 15-26 range also offers customers state-of-the-art monitoring via a simple Ethernet connection thanks to an integrated Elektronikon controller, which provides service and warning indications, error detection and optional enhanced remote monitoring features. In addition, the new compressors are remarkably compact and easy-to-install, and thus represent a true plug-and-play solution, making them ideal for installation companies and OEMs.
To enable customers to tailor the GA 15-26 to any requirement a workshop may have, a wide range of additional options are available, including an integrated dryer and filters for high-quality air, a factory-mounted receiver and various solutions for extreme climates.