New Design for Plunger Pump: Splitted Gear Box and Improved Maintenance Possibilities.
Lewa plunger pumps according to API 674 are used wherever high hydraulic power is needed, especially in the oil and gas sector and the process industry. These pumps are characterized by their compact construction and low weight, which is particularly significant for offshore installations. To meet the special requirements of customers even better, Lewa now offers a new generation of pumps with splitted gear housings.
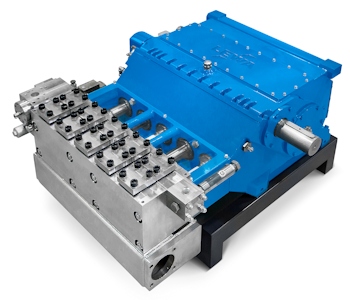
The divided gear housing of the new quintuplex pump permits the use of a fully balanced crankshaft and facilitates maintenance. (Image: Lewa)
This special feature significantly facilitates maintenance, permitting the use of a fully balanced crankshaft which generates less noise and vibration, thus reducing wear. The power range was also extended with two quintuplex plunger pumps.
The very short design of Lewa plunger pumps is made possible by the special alignment of the plunger and crosshead. These pumps also have outstanding efficiency, low energy consumption, and a long service life. The new structure with the splitted gear housing and the fully balanced crankshaft doesn t just reduce wear, but also particularly facilitates maintenance. The design of the pump also permits the maintenance of components without disassembling the process pipeline. The crankshafts are drop-forged and shot-blasted, leading to a homogeneous grain structure and low stress level. The integrated gear unit is self-adjusting and both the crankshaft and the pinion shaft are practically free of axial load.
Lewa plunger pumps are very powerful and work with volumetric accuracy. Their large valve cross-sections make the suction pressures required comparatively small. This mostly eliminates the need of a booster pump. Starting at a power of 15 kW, flexible use is possible at different drive speeds up to 800 kW, at pressures of up to 3,500 bar and a maximum flow rate of 290 m3. They are especially used for uncritical fluids like glycol, methanol, or inhibitors that are similar to water in terms of their viscosity.
Now both quintuplex variants, the G5K 500 and G5K 800, are available with maximum power of up to 800 kW. By increasing the number of plungers, the size of the individual components can be reduced for the same hydraulic power. That leads to a reduction in weight, in turn facilitating maintenance. They also achieve a low residual pulsation of about seven percent, thanks to the five plungers.
Simple maintenance and great flexibility
To protect the gear unit from low oil levels and excessive temperatures, the pump is monitored by default by a temperature and pressure switch. In the oil and gas industry, this is often implemented using transmitters. Within the gear housing, the crosshead pins and plain bearings are supplied by an integrated pressure oil lubrication system, so no additional systems are required. Because all the oil seals are accessible from outside, no gear oil needs to be drained during maintenance tasks, which has a beneficial effect on downtime. The pump head is equipped with an innovative plunger seal. Pressure and/or spring support of the seal packing allows a long service life and high availability. The gland packing is entirely maintenance-free; it never requires adjustment of pretensioning or repacking. Any packing leaks are returned internally, so no external pump is needed for returning the leakage back into the suction line and no monitoring is necessary.
Due to the modular construction, a pump can be configured that meets the requirements resulting from the application. Different pump head designs and valves are available for this purpose. The pump head design makes it possible to exchange the conversion kit, that is, the plunger and stuffing box, thus adjusting the volume conveyed and the discharge pressure over a certain range. All pumps are optimized for operation with speed controlled electric motors and/or diesel engines, but of course they can also be operated without a frequency converter. The maximum regulation range is between ten and one hundred percent of the rated speed. Depending on the application and/or the fluid, a wide variety of materials is available for selection. A number of different connection geometries and several options for monitoring and flushing are also offered.
Source: LEWA GmbH