Deprag Schulz: DCAM Assembles Ultra-efficient Heating Pump
Old heating pumps are secret power guzzlers. Few people think about these hidden “service providers” when seeking to save on electricity. Even with oil and gas heating systems, electric pumps ensure that hot water circulates from the boiler to the radiators and the hot water points.
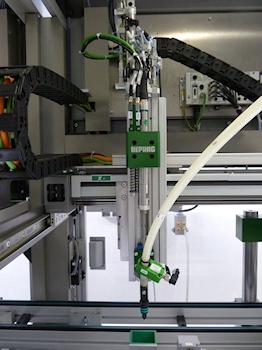
Screwdriver Function Module (Image: Deprag Schulz)
Many old pumps operate round the clock, even if no water is being heated or drawn off. On the other hand, modern, intelligent heating pumps only switch on when they are needed. That represents an energy saving of up to 70 percent. The new generation of pumps - known as ultra-efficient pumps (energy efficiency class A) - uses 400 - 700 kilowatt hours less energy. So it is not just consumers’ electricity bills that go down, but experts calculate that 240 kilograms less of climate-harming CO² per year is released into the atmosphere. Incentive programs have therefore been set up, with the aim of hastening the change to improved pumping technology. New EU directives also aim to ensure that efficient heating pumps are introduced rapidly.
For pump manufacturers this break-through signifies a massive challenge. On one hand the development means that conventionally designed pumps are “out” but on the other it is not yet clear how this new trend will impact the market in terms of production rates and sales figures. The trump card here is flexibility in production. At MOTEK 2013, the international trade show for production and assembly automation, where over 1000 exhibitors and 35,000 visitors will be meeting in Stuttgart between 7 and 10 October, Bavarian automation experts Deprag Schulz will be providing system solutions to cope with such problems. The automated assembly of control units for modern efficient heating pump technology will be one of the central themes at the Deprag stand. Using two highly reliable DCAMs (Deprag Compact Assembly Module), the mid-sized machine construction company will be demonstrating assembly solutions for flexible, cost-efficient and reliable production processes.
The DCAM was born at a time when mobile phones were still being assembled manually. The company that could produce faster and more cost-effectively had the advantage. The Deprag assembly station for industrial production came onto the market and since that time has become established worldwide. Over the past 25 years the engineers at Deprag have consistently worked to enhance this much-loved assembly platform. Now the DCAM is even available “off the peg”. It is available in modular form, and has been optimised to ensure that it is even more cost-effective. At MOTEK 2013 Deprag will be demonstrating, on two DCAMS, the assembly process for the control unit that forms the heart of an energy-efficient, intelligent new generation heating pump.
In the DCAM assembly solution sales manager Jürgen Hierold sees the most economical answer to many of the problems currently faced by manufacturers and not just those producing heating pumps. “When production rates fluctuate, where there are lots of different product variants and when a product’s life cycle is short, the DCAM modular assembly platform is the most appropriate solution. A DCAM links effectiveness with the highest possible process reliability. With its modular and flexible platform design this assembly cell, combined with the freely programmable X-Y axes, can be deployed flexibly for an extremely wide variety of assembly tasks.”
Deprag engineers have built a linear transfer system with return, in a loop formation, on which the most important assembly steps are demonstrated on a sample component. The sample product to be assembled on the platform is a control unit (ECU) for an intelligent heating pump.
The upper and lower halves of the component arrive at a manual workstation on a workpiece carrier where a worker uses four screws to fasten a PCB which has been prefitted onto the lower half. A Minimat-EC manual screwdriver is used for this task, guided by a position control stand, while a fully automated feeder ensures that the screws feed to the correct position. Sales Manager Jürgen Hierold explains: “All the relevant components come from our own in-house design and manufacturing facilities. DEPRAG covers the entire value-added chain.” The user-friendly process control system, which guides the worker through the fastening procedure via the on-screen display also comes from the automation experts based in Amberg, Germany. If the controller assesses the workpiece as OK the operator sends the component to the next workstation.
Now the first DCAM gets to work. On this compact workstation visitors to the exhibition will be able to see the bushings being pressed together - fully automatically. Four bushings are now pressed onto the upper half of the electronic component. For this task the vacuum spindle on the press-in tool travels towards the bushing auto feed system which uses a pick and place process to prepare the relevant bushing, then “fetches” the bushing and passes through a visual inspection station where the geometry and position of the bushing is measured. The dynamic display of test results appears on the touch screen. If the measurement is OK, the press-in tool moves above the press-in position and presses the bush in. A force-stroke monitoring unit controls the process and ensures the necessary process reliability. The process is repeated four times until this assembly step is complete. The linear handling system now places the upper part of the control unit onto the lower half, and the workpiece carrier moves it on to the next station - the second DCAM.
At the second DCAM on the exhibition stand DEPRAG will be demonstrating a typical screwdriving process. The upper half of the ECU is screwed onto the lower half, fully automatically and with total reliability. Sales Manager Jürgen Hierold adds: “Our screwdriving function modules are designed to ensure optimum process reliability. Torque, angle, speed, dwell time and direction of rotation can all be programmed as required within the performance spectrum of the screwdriver spindle concerned and adapted individually to the screwdriving task in hand.” The world-renowned EC stationary screwdrivers are equipped with brushless EC motors and operate virtually maintenance-free. A DEPRAG AST10 automatic sequence controller with integral web server is used in combination with a MINIMAT® EC screwdriver - which makes it very easy to create and configure screwdriving programs in the Linux operating system environment.
Once the screwdriving process has finished (a automatic screw feed system supplies this step of the process by shooting the requisite screws through a hose), the second workstep is now complete. The assembly platform includes a function whereby the PCB that was previously assembled at the manual workstation is inspected in a fully automated process. The workpiece carrier is lifted and fixed in position. Now the test adapter can make contact with the PCB. If this functional test is positive, the DPU200, which is controlling the processes on both the DCAMs, indicates on the screen that the fitted component is “OK”.
Like all DEPRAG PROCESS Control modules, the DPU200 is also equipped with DCOS software, available in various standard packages. Jürgen Hierold points out the benefits: “This software contains the skills and expertise gained from decades of planning, execution and implmentation of custom assembly systems along with the necessary measuring technology to ensure process reliability. DEPRAG engineers know all the problems that Manufacturers and workers face, and what they want in order to carry out their assembly tasks. This complex knowledge has been assimilated into specially developed DCOS software.” Only people who enjoy their work will do it well. This is why in all its design work DEPRAG places great importance on the best possible Human Machine Interface (HMI), including in the DCOS software. The control unit is designed to be very user-friendly in operation. The uncluttered colour touch-screen can be operated by touch with a finger or stylus.
The intelligent heating pump control unit is now fully assembled. At the DEPRAG stand for Motek, it now travels to another manual workstation, where it is dismantled and prepared ready for the next demonstration. In the real world, this station would probably be used as a repair or rework station.
The clients focus is of course on the economy factor for their future assembly systems. Jürgen Hierold: “Our work cell has been frequently copied. We make no compromise when it comes to quality. So our machine bases are manufactured from formed steel members with torsion-resistant screw fastenings. These powder-coated steel frames are able to assure the internationally recognised stability and durability of the platform.” DEPRAG uses its own axes - developed in-house - for the assembly cell: The design engineers opted for high-quality axis modules consisting of linear axes with tooth-ring drive and, on request, a Z-axis with ball screw. The engineers are unanimous in stating that it is only in this way that the system will cope with the typical stresses, such as the reaction to torque and the mass loads incurred by screwdriving assembly work. Jürgen Hierold asserts: This is what achieves the high level of functional repeatability and the legendary reliability of this assembly platform.
The new standardised DCAM is available in two versions. Version A provides a maximum effective distance of movement of 400 millimetres for the X-axis, and 250 for the Y-axis. In version B the X and Y axis each travels up to 600 millimetres. An optional Z-axis, likewise developed for use in the DCAM, and which can also be easily retrofitted to an XY system, has a useful travel range of 160 millimetres and requires less than a second for its total stroke.
Jürgen Hierold points out: “By means of standardisation the world-renowned DCAM is at last available at a fixed price and with shorter delivery times. Without compromising the successful concept in any way, the technology that has been well proven and constantly enhanced over the past 25 years, is now available in standardised modules, to the benefit of customers.”
Source: Deprag Schulz GmbH u. Co.