Micropumps at the Cutting Edge of a Specialist Glass Manufacturing Process
Today’s building design and architectural trends demand constant innovation in materials manufacture, especially for prestigious or high profile commercial projects.
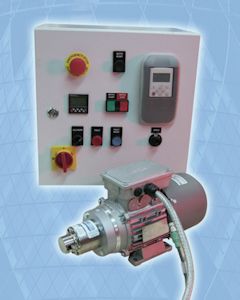
Michael Smith Engineers
As a consequence of this manufacturers are required to continually develop materials which meet the challenges of cutting-edge design and energy efficiency. A good example of this is the demand for specialist glass panels for cladding the outside of buildings to maximise light and heat, such as those manufactured by Huddersfield based Specialist Glass Products (SGP). Pumping specialists Michael Smith Engineers has recently supplied a Micropump and inverter system to SGP which has successfully met the complex demands of a specialised application that had proved to be too challenging for a traditional mechanically sealed pump.
The process involves making reinforced laminated double-glazed panel sections varying in sizes up to 5 metres and with some of the panels needing to be curved. Glass panels with extremely low thermal conductivities are placed into specially designed mounts inclined at one end and then a second panel is suspended and lowered over the mounted panel. The edges are aligned and fixed spacers are inserted around the edges of the two panels, a sealing strip is then applied around all sides. The interior ‘sandwich’ section is then filled with a pre-determined volume of UV sensitive urethane based acrylic monomer resin. This filling process is done by a batching pump, with total volume calculated via a batched metering system, with the flow rate also being adjusted during the process.
The flow rate adjustment is critical because the UV resin must be introduced between the two panels at exactly the right speed.
If the flow is fractionally too fast the mixture picks up air bubbles caused by drag on the glass surface and the surface tension of the liquid resin. These bubbles take a long time to move up the glass panel before they can be burst and released at the open end of the panel, if they don’t the complete panel has to be scrapped.
Once an initial flow rate to the base of the panel is established and the base edge of the panel is confirmed as sealed, the flow rate is then gradually increased to ensure that no bubbles become entrained. The filling operators are skilled in watching the flow of the resin and adjusting the feed rate to the maximum possible in order to reduce manufacturing time. Towards completion of the filling process the flow is reduced to ensure an even spread of the resin in the top of the panel, the top edge is then sealed and overhead UV lamps cure the resin for 20 minutes up to a few hours, depending on the size and thickness of the panel.
The key elements of the design brief for Michael Smith Engineers were; provide a pumping system which would deliver a smooth, even and accurate output to reduce the chance of entrained bubbles, incorporate a sealless magnet coupling so resin will not be exposed to air causing it to harden in the pump, ease-of-use for the operator and automatic slowing down of the pump at the end of the batch to prevent overfilling. Specifically, the need was for a pumped batch metering transfer system for acrylic monomer resin with a viscosity of 100 cP. This was designed to draw the resin from the base connection of a 1000 litre IBC at a flow rate of between 0.1 to 1.2 lit/min in metered batch sizes of 0.1 to 10 litres with stop, start and resume controls.
The system comprised a Micropump with an inverter controlled motor with integral dual channel encoder for operating at speeds up to 2100 RPM. Following installation and operation the pumping system’s filling accuracy was measured at +/-1% of batched volume and thanks to the smooth and accurate delivery of the resin combined with optimum speed control, the problems of entrained bubbles were eliminated.
A second system has subsequently been supplied to batch meter a similar acrylic monomer resin, but with a viscosity of 0.8 to 2 cP.
The successful deployment of a Micropump on this challenging application is a good example of the characteristics of this unrivalled range of range of external gear pumps which, with variety of available options, allows users to specify a pump which is tailored specifically to their application. The Micropump range comprises 9 series of pumps covering cover flow rates from as low as ml/hr, up to 40 lit/min at maximum discharge pressures between 5.2 and 8.5 bar, depending on the model and the fluid. They are available in a choice of metallurgies including stainless steel and Hastelloy, while a range of different gear materials can be specified to best suit the liquid being pumped and / or the duty parameters. They can also be supplied with different porting arrangements.
All models have magnet drives so the risks of process fluids leaking are eliminated ensuring that operators have the benefits of reduced environmental, health and safety and chemical handling issues.
Source: Michael Smith Engineers