Armstrong Gets Down to Business With Packaged Plant Rooms for Lydiard Fields
Offsite manufactured plant rooms from Armstrong have reduced installation times for two top quality new office buildings at the prestigious Lydiard Fields Business Park.
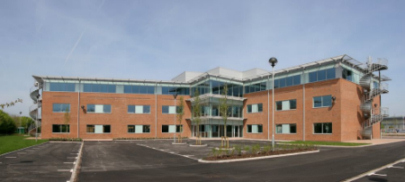
Pictured is Auckland House - one of two new office buildings on the Lydiard Fields Business Park with offsite manufactured plant rooms from Armstrong
In addition to streamlining the schedule, the variable speed drive pumps at the heart of the HVAC systems will ensure long-term energy efficiency by automatically reacting to the heating and cooling requirements of each building.
Washington House and Auckland House represent the second of three phases at the Lydiard Fields Business Park in Swindon, located adjacent to the M4 motorway. Developer BAM Properties purchased the site in May 2004 and has already let some of the previously completed buildings, including Canberra House and Kingston House. When planning the final two projects, BAM – which used the construction arm for the building - and its M & E contractor Renelec Building Services, decided that an offsite construction approach would have significant benefits and approached Armstrong to provide packaged plant rooms.
Armstrong constructed the two plant rooms at its production facility in Halesowen, West Midlands. The plant rooms incorporate HVAC systems for chilled water, hot water and heating. Incorporation of variable speed drive pumps means that the site will be able to minimise energy consumption. The Armstrong IVS pumps have built-in inverters which automatically calculate the building load throughout the day and night, matching the pump speeds to the demand. These features, along with high efficiency low NOx boilers and a ‘Thermal Wheel’ for ventilation heat and cool recovery have contributed to the offices receiving a ‘Very Good’ rating from BREEAM.
Manufacturing the plant rooms in the factory instead of at the construction site enabled the HVAC element of the project to progress concurrently with the build, rather than having to wait until the completion of the major works. On the date required, the plant rooms were delivered to site fully-assembled, in enclosures, requiring only final connections. This removed risks of bottlenecks such as adverse weather conditions and, as the work could be completed in the more easily controlled environment of a factory, the health and safety risks for the project could be minimised.
The incorporation of variable speed drive technology has reduced the lifetime cost for the installation and enables BAM to offer the occupiers the benefit of reduced energy bills and improved carbon footprint.
“Potential occupiers of office space are increasingly aware of the cost and CSR impacts of commercial buildings” said Steve Cooper, Director of Renewables and Sustainability at Armstrong. “The equipment choice for the Lydiard Fields office buildings established a long-term basis for reducing carbon footprint by eliminating wasted energy associated with fixed speed pump systems.”