Vane Pumps Cope With Pressures of Tough Applications
The LVP Series of Vane pumps, recently introduced by Michael Smith Engineers, offer important benefits particularly when challenging applications occur involving chemicals or liquefied gases.
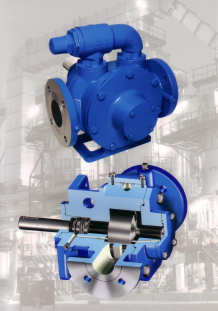
For example, in this type of pump design vanes extend from slots in the pump rotor and these help to ‘sweep’ liquid through a cam-shaped cavity. This ensures very low slip and high volumetric efficiency at all points on the performance curve, which contributes to a longer pump life and low life-cycle cost.
The LVP range of pumps covers flow rates up to 36m3, pressures up to 14 bar and the ability to handle liquids with viscosities from 0.1 to 500 cSt. They are also designed to provide smooth, non-pulsating, low-shear flows and offer superior suction lift capability, short-term dry-run capability, capacity proportional to speed and reversible direction of flow.
LPV pumps use materials which ensure optimum durability and long-life performance. For example, they are manufactured with surface hardened stainless steel casings as standard and feature a hardened chrome oxide coated shaft which turns within a silicone carbide sleeve bearing.
Also, the pump’s self-adjusting, solid PEEK plastic vanes and push rods provide superior vacuum capabilities.
To ensure easy installation the pumps have standard ports to enable simple fitting of gauges or transducers, top-mounted adjustable pressure relief valves, which eliminates the need and expense of return-to-tank systems. A rotatable casing with motor mount option on the two smallest models in the range, permits either horizontal or vertical porting.
Typical applications for Viking LPV pumps will include transferring corrosive and thin liquids that are compatible with stainless steel, yet cause unacceptable corrosion on cast iron pumps. For example, in chemicals manufacturing where users run many different liquids through their pumps, such as acids, alkalis, alcohols, solvents and aqueous solutions, yet require maximum corrosion protection.
Source: Michael Smith Engineers